POS Systems & Cash Registers
for Restaurants, Retail & Services
OktoPOS is the ultimate all-in-one cash register system and store management software, specifically developed for retail, hospitality, and the service sector. It combines advanced hardware and software solutions to offer the most comprehensive set of features on the market. Whether it's cash registers, printers, self-checkout and self-order terminals, customer apps, employee management, inventory management, or e-menus – OktoPOS covers all your needs.
Thanks to its customizable setup, you can select the modules that are specifically needed for your particular requirements. This allows you to create a tailored system that not only optimizes your operational processes but also enhances efficiency and customer satisfaction.
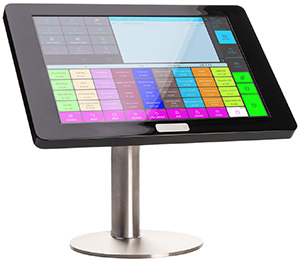
Benefit from a system that is flexible, scalable, and perfectly tailored to the needs of your business. With OktoPOS, you are well-equipped to efficiently manage your operations and quickly respond to the ever-changing market conditions.
More than just a Cash Register
OktoPOS stands at the forefront of modern branch management systems by offering a comprehensive platform that extends far beyond the functionalities of a traditional cash register. Thanks to its numerous interfaces, OktoPOS can integrate and process a variety of data sources, making it ideal for managing branches in various sectors.
License & Updates
The OktoPOS system is distinguished by its continuous development, supported by a web-based approach. This ensures that the system always remains at the cutting edge of technology, giving you access to the latest features and security updates.
The licensing of the OktoPOS system is on a monthly basis and includes all updates and developments. This model offers a flexible and cost-efficient solution, allowing you to use the system without long-term capital commitment. You benefit from a clear cost structure without unexpected expenses for software updates, which significantly simplifies planning and budgeting.
With OktoPOS, you invest in a future-proof solution that grows with your business and adapts to changing market requirements while continuously integrating technological advancements into your business processes.
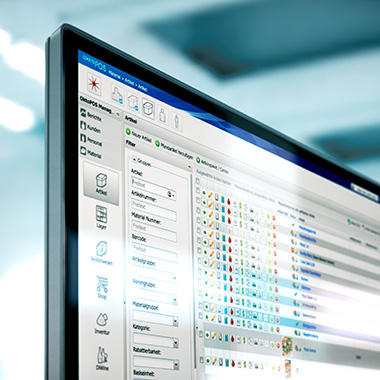
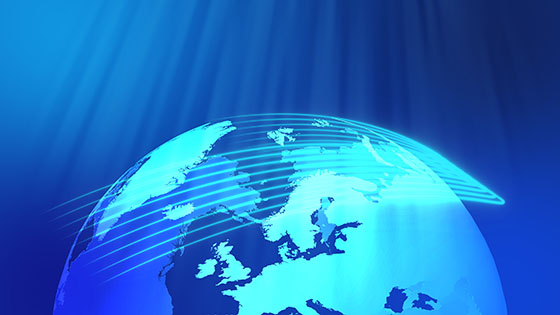
Mobile and Global Management
The OktoPOS Manager, the system's central management tool, utilizes a central database to control all operational processes through a single platform. This not only simplifies the organization and maintenance of your business processes but also allows you to manage your business from anywhere in the world, as long as a secure internet connection is available.
The support for multiple languages and currencies makes the OktoPOS system particularly attractive for the international market. Whether you are managing local stores or global branches, OktoPOS offers the flexibility and scalability needed for efficient and effective branch management. Use OktoPOS to optimize your business processes and gain a clear overview and control over your operations, regardless of your location.
24/7 Support
Call our 24-hour hotline at any time. Through our remote maintenance, we solve more than 99% of all inquiries quickly and efficiently right on your first call.
If you are interested or have any questions, please contact us and we will put together your system for you.